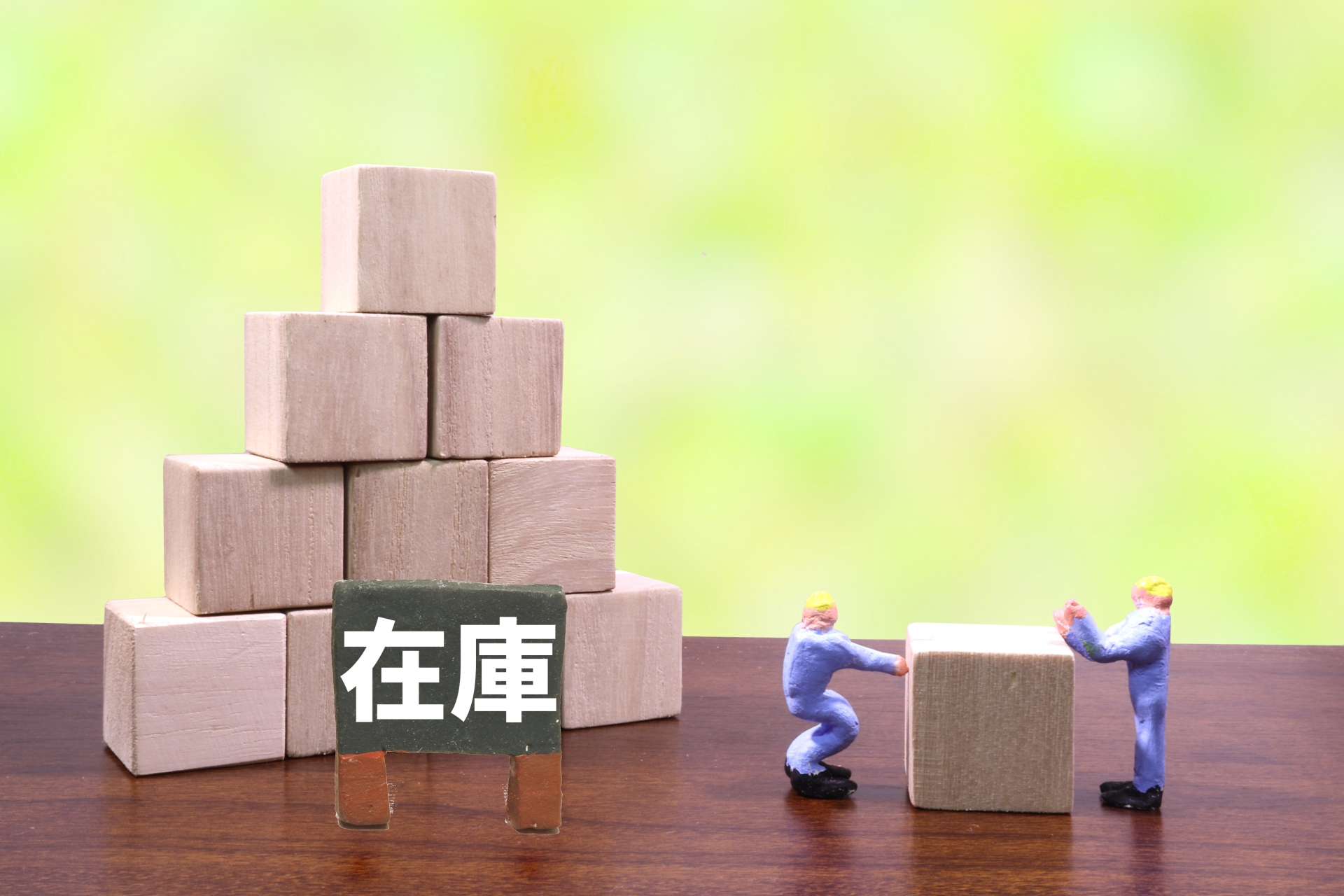
目次
定量発注方式とは
定量発注方式とは、一定の在庫量が減少したときに、決まった量だけ発注する方式のことを指します。商品の販売や使用にあたって、在庫管理は適切に行わなければならない重要な要素の一つです。
定量発注方式の定義と特徴
定量発注方式は「発注点」と「発注量」の2つの要素で構成されています。発注点とは、商品の在庫が一定の量まで減少した際に発注を開始するための点です。一方、発注量は一度に発注する商品の数量を指します。これらを適切に設定することで、無駄な在庫を抑えつつ、ニーズに応じた供給を可能にします。
定量発注方式の特徴は、在庫管理の手間を削減でき、安定した供給を維持できる点にあります。一方で、需要の変動に対応するのが難しいため、欠品や過剰在庫のリスクを伴います。
適切な発注点と発注量を設定するためには、過去のデータや市場の動向を基に計算することが一般的であり、これには様々な計算式が用いられます。
定量発注方式の流れ
定量発注方式の流れは、まず、発注点と発注量を設定します。これらは商品の種類や需要の変動、納品までのリードタイムなどによって異なります。
次に、発注点に達すると、事前に定められた発注量分の商品を注文します。そして、商品が納品されて在庫が補充されると、再び発注点に達するまでの間は発注を行いません。
これにより、一定の在庫量を維持しつつ、安定した供給の確保を行うことができます。
定量発注方式と他の発注方式との関係
定量発注方式と同時に利用されることが多いのが、定期発注方式です。これは、特定の期間ごとに一定量の発注を行う方式で、これにより発注の手間をさらに節約し、仕入れの安定化を図ることができます。
一方で、発注量が固定されているため、需要の変動に柔軟に対応することが難しいという欠点もあります。そのため、これら二つの発注方式は相補的な関係にあると言えます。
また、ABC分析などの手法を用いて商品を分類し、それぞれの商品に最適な発注方式を適用することで、更に効率的な在庫管理が可能になります。
定量発注方式を選ぶ理由
定量発注方式を選ぶ理由としては、まず簡易さと手間の削減が挙げられます。発注量と発注点を設定すれば、それ以降は発注点に到達する度に自動的に発注が行われます。また、これにより在庫切れを防ぎつつ、必要以上の在庫を持つことなく経済性を確保することができます。
しかし、需要の急な変動に対応しづらいという欠点があります。そのため、需要が比較的安定した商品や、リードタイムの長い商品などに適用されることが多いです。
各商品の特性やビジネス環境により、定量発注方式と他の発注方式を適切に組み合わせることで、最適な在庫管理を行うことが求められます。
定量発注方式の計算方法
定量発注方式では、主に「発注点」、「安全在庫量」、「経済的発注量」の3つが重要なパラメータとなります。その算出方法を詳しく解説します。
計算式が伴う内容ですが、適切な発注を行うために必要な知識であり、理解しておくことで業務の効率化を図ることが可能となります。
これらのパラメータを用いることで在庫管理がスムーズになり、在庫切れや過剰在庫による損失を未然に防ぐことが可能となります。
発注点の決定方法
発注点とは、商品の再発注を行うべきタイミングを示す指標です。具体的には「1日の平均使用量×発注リードタイム + 安全在庫量」という計算式で算出されます。
1日の平均使用量は、過去のデータから算出でき、発注リードタイムは商品が発注から納品までに要する時間を表します。これらを掛け合わせた値に、安全在庫量を加えることで発注点を求めます。
正確な発注点の計算は在庫切れを防ぎ、顧客満足度の向上につながります。
安全在庫量の算出方法
安全在庫量とは、予期しない需要や供給の変動に備えて保持しておく在庫の量を指します。
具体的には「安全係数×使用量の標準偏差×√(発注リードタイム+発注間隔)」という計算式で算出されます。ここで、安全係数は需要の変動幅をカバーするための係数で、事業者が自身のリスク許容度に応じて設定します。
適切な安全在庫量を保持することで、突発的な需要増や供給遅延に対処することができ、結果的に安定した業績を維持することにつながります。
経済的発注量の計算
経済的発注量とは、1度の発注で注文すべき数量を示します。
「√{(2×1回あたりの発注費用×年間需要量)÷(在庫品の単価×在庫費用率)}」を計算することで求められます。
経済的発注量を適切に設定することで、発注コストと在庫保管コストの最小化を可能とし、経営効率の向上に寄与します。
定量発注方式の計算例
具体的な計算例として、「1日平均使用量が50個、発注リードタイムが5日、安全在庫量が30個の場合の発注点」を求めます。
これにより、「50個×5日+30個=280個」となり、在庫が280個になった時点で商品の発注を行うのが適切とされます。
このように具体的な数値を当てはめることで、実際の業務に活用することができます。
定量発注方式のメリット・デメリット
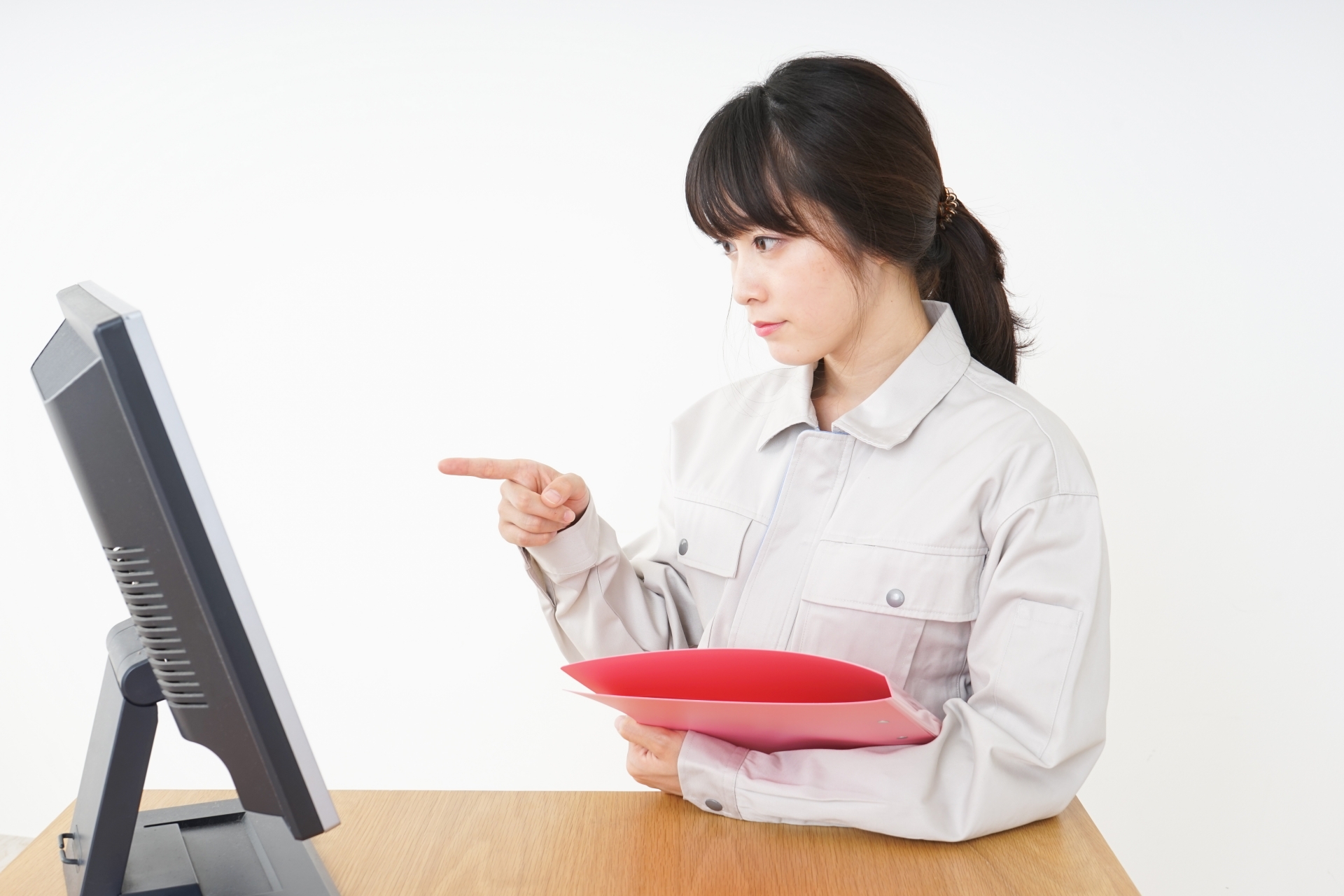
在庫の管理はビジネスの重要な側面を占めています。それぞれの商品や状況に応じて発注方式を選択することが必要です。定量発注方式について、そのメリットとデメリットを考えてみましょう。
定量発注方式の主なメリット
定量発注方式の最大のメリットは、発注手続きの効率化です。在庫が予め設定された量(発注点)まで減ると自動的に定められた量を発注するため、人間が常に在庫を監視して発注する必要はありません。これによって業務効率が上がります。
また、発注を均一化することもメリットです。一定量を一定のタイミングで発注することで、在庫の変動を抑えられるため、予測性が高まります。
さらに、発注作業が自動化されるため、ヒューマンエラーを防ぐこともできます。誤って発注数を間違えるリスクが減少します。
定量発注方式の主なデメリット
一方、定量発注方式のデメリットは需要の変化に対応できない点です。需要が予想より増えた場合、発注量が固定化されているために急な需要の増加に対応できず、欠品のリスクが増えます。
逆に、需要が予測より減少した場合は、過剰在庫につながる可能性があります。これはキャッシュフローを圧迫したり、在庫管理コストの増加につながります。
また、製品ライフサイクルの変動にも対応することが難しくなります。新製品や季節性のある製品など、需要が急激に変わるものの発注には不向きな方式といえます。
メリット・デメリットを踏まえた適用シーン
これらのメリットとデメリットから、定量発注方式は需要の安定した商品や始動部品などで効果的と言えます。安定した需要が見込まれ、在庫状況が予測しやすいものに適用すると効率よく運用することが可能です。
一方、市場動向や季節の変動などによって需要が急激に変わる商品には定期発注方式や需要予測に基づいた発注方式を併用するなどする方が適しています。
つまり、商品や市場状況、需要の変動要因を踏まえた上で、最適な発注方式を選択することが必要です。
定量発注方式の改善点
デメリットを克服するために、さまざまな改善点を見つけることができます。例えば、発注点や発注量を定期的に見直す、あるいは動的に調整する仕組みを構築することです。
また、使用量の変化をリアルタイムに把握するために、在庫管理システムを活用するといった対策も挙げられます。
これらを踏まえた上で定量発注方式を適用し、在庫の適正化と業務効率の向上を図ることが重要です。
ABC分析と定量発注方式
定量発注方式と一体どのようにABC分析が関わっているのか、この章ではその繋がりを詳しく説明していきます。
ABC分析とは
ABC分析は、商品の在庫や商品毎の販売数を評価し、管理の優先度を決定するという方法です。具体的には、商品を「Aグループ」、「Bグループ」、「Cグループ」の3つに分類します。これはそれぞれ、「主力製品」、「重要度が中程度の製品」、「重要度が低い製品」に対応します。この分析方法を用いることで、在庫管理という視点で最も重要な製品を見抜き、それに応じた発注量を考えることが可能になります。
ABC分析の誕生は膨大な商品の中から重要な商品を選び出すため、また手間とリソースを計量化して管理するための手法として生み出されました。
この分析によって商品の優先度が明確になるため、極めて効率的な資源を割り当てが可能になるのです。
ABC分析と定量発注方式の関わり
ABC分析と定量発注方式の間には密接な関係があります。というのも、これは定量発注方式は発注量を決めるにあたり、製品の重要性や需要を見極める必要があるためです。具体的には、需要が高い主力製品(Aグループ)は常に必要な量を供給できるよう、頻繁に大量の発注を行うべきです。
一方で、需要がそれほど高くないCグループの製品については、過剰な在庫を抱えるリスクを避けるため、少量もしくは定時的な発注を行うべきです。
ABC分析を行うことで、これら製品ごとの発注量を計画することが可能になり、結果として定量発注方式を効果的に活用できるからです。
ABC分析による在庫管理の例
具体的な在庫管理の例として、一つの会社が600種類の商品を取り扱っていると仮定します。このときABC分析を行うと、売上の大部分を占める主力製品(A群)が60種類、同じく売上に貢献する中程度の製品(B群)が90種類、売上貢献度が低い製品(C群)が450種類となりました。
この場合、会社はA群の商品に対しては頻繁且つ大量の発注を行い、B群の製品については平均的な頻度と量で発注を、C群の商品に対しては必要最低限の発注を行う形になるでしょう。
これにより、各製品の需要と在庫、そしてコストを効率的に管理することができます。
ABC分析を活用した定量発注方式の成功例
成功事例として、大手家電製品メーカーがABC分析を採用し、売上の70%を占める主力製品群(A群)を特定。特定したA群製品に対して定量発注方式を採用し、他グループの製品に対しては必要最低限の発注を行う方式に変更しました。
その結果、主力製品群(A群)の在庫切れがなくなり、売上向上に直結。一方、B群とC群の製品では過剰在庫が大幅に削減され、結果的に合計で在庫管理コストが20%以上も削減されました。
これにより明らかなように、ABC分析を用いた定量発注方式は、在庫管理の効率化とコスト削減に大いに寄与することができます。
定量発注方式の最適化
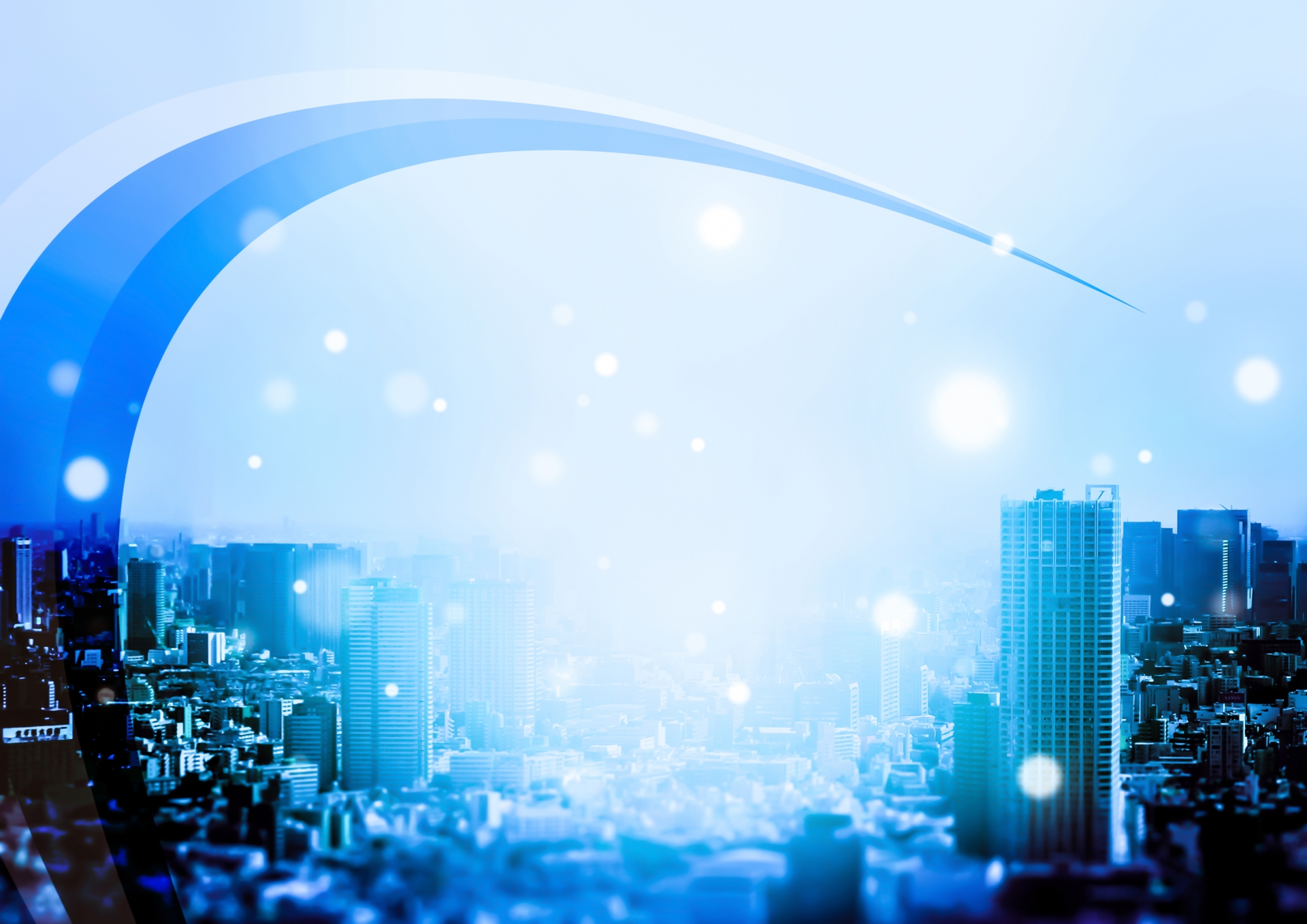
定量発注方式の最適化は、企業の運用体制の改革をもたらし、効率化に大いに貢献します。しかし、最適化を実現するには需要予測の精度や最新技術の活用が欠かせません。
各段階の適切な手法を知ることで、定量発注方式を現代のビジネス環境に適応させ、更に発展させることが可能です。それでは具体的な方法を見ていきましょう。
需要予測と定量発注方式の関係
需要予測は、定量発注方式の最適化に必要不可欠な要素です。需要予測が進化することで、発注点と発注量をより正確に予測することが可能となってきました。
さらに適切な必要量と安全在庫量を計算するためには、過去のデータと未来予測が重要です。それによって過剰在庫や欠品を未然に防ぎ、コスト削減につながります。
IoTやAIを活用した定量発注方式
IoTやAIの活用で、定量発注方式はより高度化しています。これらの技術はデータをリアルタイムで収集し分析することが可能で、発注点の高精度化が期待できます。
AIは特定のパターンを精度高く見抜く能力を有しており、莫大な情報から有用な知見を引き出すことができます。これにより定量発注方式の精度向上が図られます。
最適化技術の進化と定量発注方式
未来の需要予測や在庫管理の最適化には、最新の最適化技術が重要な役割を果たしています。これらの技術は定量発注方式の最適化に貢献しており、適切な発注タイミングを見極める能力を向上させています。
また、最適化技術の進化は在庫コストを削減し、ビジネスの成長を推進します。エンドツーエンドの最適化を実現するためには、このような最新の技術は欠かせません。
最適化を行う際の注意点
定量発注方式の最適化を行う際は、適切な戦略と計画が不可欠です。 企業の在庫管理目標や需要予測の精度、技術の導入レベルなどを考慮することが重要です。
また、新たな技術を導入する際には、その導入コストや時間、スキルを習得するための教育コストなども考慮しなければなりません。
このように、定量発注方式の最適化には計画性と戦略性が求められます。業務効率化に向けた取り組みとして、最適な手法を選び、実行に移していきましょう。
定量発注方式の実践ガイド
定量発注方式を活用することで、リードタイムの管理や在庫コントロールなどに有用です。しかし、導入にあたり、適切な準備を行うことが重要となります。
定量発注方式の導入準備
まず、発注点と発注量を設定するために必要な数値を確定します。特に、一日の平均使用量、発注リードタイム、安全在庫量などの計算には十分注意が必要です。
また、発注費用の算出も重要です。ここで一回あたりの発注費用や在庫品の単価、在庫費用率などのパラメーターをきちんと設定します。
さらに、ABC分析を活用し、商品の重要度や優先度を判断します。これにより発注方式の選択が容易になります。
ステップバイステップでの導入方法
まずは、発注点と発注量を設定します。これらは定量発注方式の成功にとって重要なポイントであり、しっかりと管理してください。
次に、発注のタイミングを見極めます。繁忙期や需給バランスの変動を考慮し、適切なタイミングで発注するようにします。
そして、発注後の在庫管理を行います。受注状況や在庫量のモニタリングを行い、発注点と発注量の再設定をします。
定量発注方式の運用とモニタリング
導入後も日々の運用とモニタリングが重要です。特に、発注点と発注量の適正な調整は、在庫管理の効率化に寄与します。
また、顧客要望や市場の変動に対応するため、発注リスクを最小限に抑える戦略も必要です。
さらに、定性的なフィードバックも取り入れ、在庫管理の改善に繋げることが大切です。
チェックポイントと改善アプローチ
ここでは、発注点、発注量、発注リードタイムなど、定量発注方式における重要なチェックポイントを確認します。
これらの数値が適切か定期的にチェックし、必要に応じて見直しを行います。
また、改善アプローチも重要です。例えば、ABC分析に基づいて、商品の重要度や優先度を再評価するなどのアクションを取ります。